Porosity in Welding: Identifying Common Issues and Implementing Ideal Practices for Avoidance
Porosity in welding is a pervasive concern that frequently goes undetected until it creates substantial issues with the honesty of welds. In this discussion, we will certainly discover the essential factors contributing to porosity formation, examine its detrimental impacts on weld performance, and talk about the finest techniques that can be embraced to lessen porosity occurrence in welding processes.
Usual Reasons of Porosity
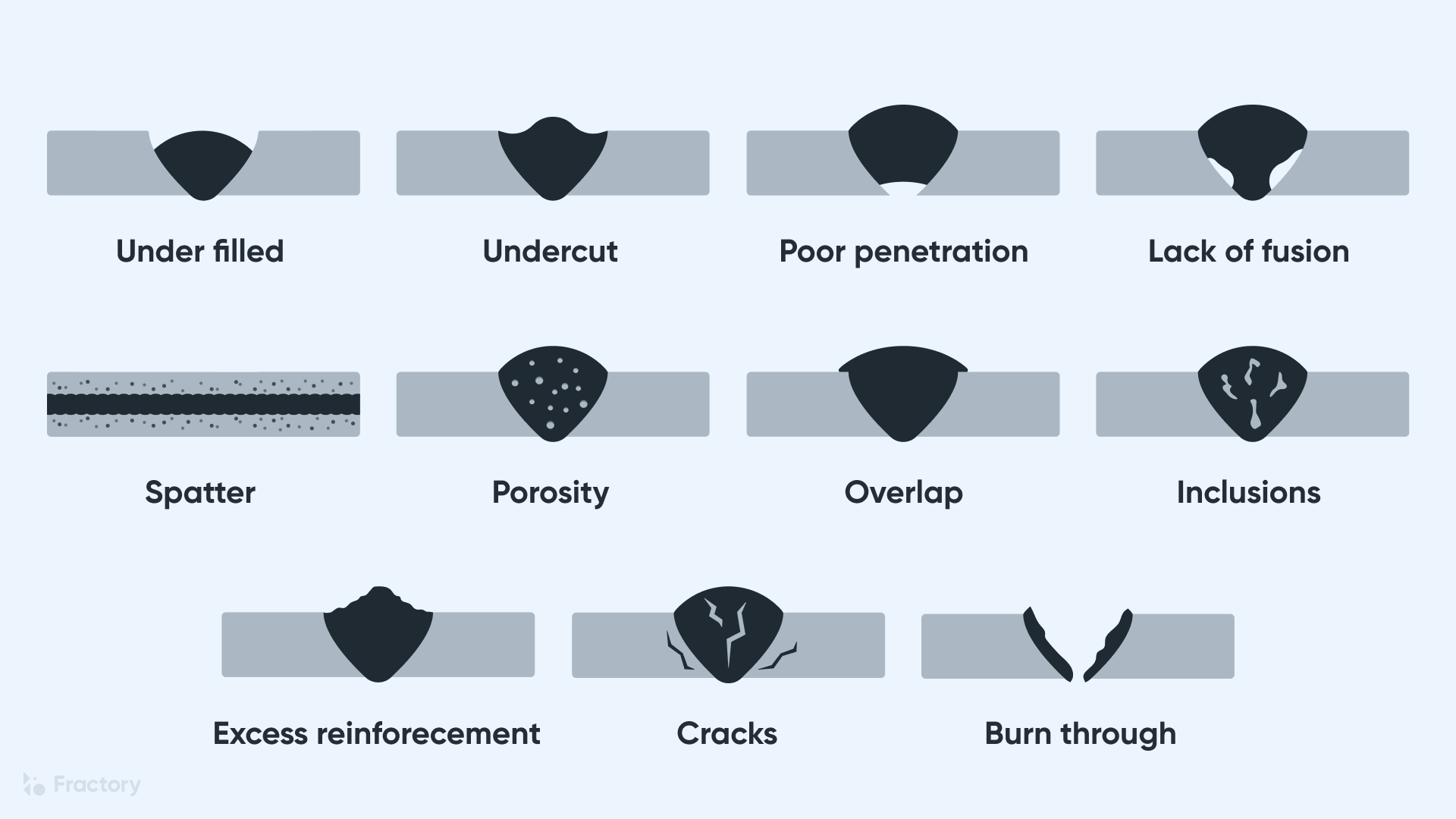
One more constant offender behind porosity is the visibility of pollutants externally of the base metal, such as oil, oil, or rust. When these pollutants are not effectively removed prior to welding, they can vaporize and end up being trapped in the weld, causing flaws. In addition, using dirty or damp filler products can present contaminations into the weld, adding to porosity problems. To reduce these common root causes of porosity, detailed cleansing of base steels, appropriate protecting gas option, and adherence to ideal welding criteria are vital techniques in attaining high-grade, porosity-free welds.
Influence of Porosity on Weld Top Quality

The existence of porosity in welding can substantially endanger the structural integrity and mechanical residential or commercial properties of bonded joints. Porosity develops voids within the weld steel, deteriorating its total strength and load-bearing capability.
Among the key consequences of porosity is a reduction in the weld's ductility and durability. Welds with high porosity degrees often tend to show lower impact toughness and decreased capability to warp plastically prior to fracturing. This can be specifically concerning in applications where the bonded parts go through vibrant or cyclic loading conditions. In addition, porosity can hinder the weld's capacity to effectively transfer forces, resulting in premature weld failure and potential safety risks in vital structures.
Finest Practices for Porosity Avoidance
To boost the architectural integrity and quality of welded joints, what particular steps can be carried out to decrease the incident of porosity during the welding procedure? Porosity prevention in welding is vital to make sure the honesty and toughness of the last weld. One reliable technique appertains cleansing of the base steel, eliminating any kind of pollutants such as corrosion, oil, paint, or wetness that could cause gas entrapment. Making sure that the welding equipment remains in good problem, with clean consumables and ideal gas flow prices, can also dramatically minimize porosity. Additionally, preserving a stable arc and managing the welding parameters, such as voltage, present, and take a trip speed, aids create a regular weld pool that lessens the risk of gas entrapment. Utilizing the correct welding method for the details material being bonded, such as adjusting the welding angle and weapon placement, can internet even more protect against porosity. Regular assessment of welds and immediate remediation of any type of issues determined throughout the welding procedure are important techniques to avoid porosity and generate top quality welds.
Value of Correct Welding Strategies
Applying correct welding strategies is paramount in ensuring the structural integrity and article source top quality of bonded joints, constructing upon the structure of efficient porosity prevention steps. Extreme warm can lead to enhanced porosity due to the entrapment of gases in the weld pool. Additionally, using the appropriate welding parameters, such as voltage, current, and take a trip speed, is vital for accomplishing audio welds with very little porosity.
In addition, the option of welding procedure, whether it be MIG, TIG, or stick welding, should line up with the specific demands of the task to make certain optimum results. Proper cleansing and prep work of the base metal, along with picking the best filler material, are also essential elements of efficient welding techniques. By adhering to these finest techniques, welders can reduce the danger of porosity development and produce premium, structurally audio welds.
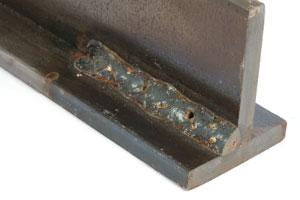
Checking and Quality Assurance Procedures
Checking treatments are vital to detect and prevent porosity in welding, guaranteeing the strength and resilience of the final product. Non-destructive testing approaches such as ultrasonic testing, radiographic screening, and aesthetic evaluation are frequently employed to determine possible defects like porosity.
Conducting pre-weld and post-weld examinations is likewise vital in maintaining top quality control requirements. why not try these out Pre-weld evaluations entail verifying the materials, equipment settings, and cleanliness of the work area to stop contamination. Post-weld assessments, on the various other hand, examine the last weld for any kind of issues, consisting of porosity, and validate that it fulfills defined criteria. Applying a thorough top quality control strategy that consists of detailed screening treatments and assessments is vital to minimizing porosity problems and guaranteeing the general top quality of welded joints.
Conclusion
To conclude, porosity in welding can be an usual issue that impacts the quality of welds. By identifying the typical reasons for porosity and carrying out ideal practices for prevention, such as proper welding techniques and testing procedures, welders can make sure premium quality and reliable welds. It is important to prioritize avoidance methods to decrease the incident of porosity and keep the stability of bonded structures.